I rarely ride on turboprops such as the ATR 72 and DHC Dash 8-400. But don’t get me wrong, I’m not afraid of flying on turboprops. In fact, I’ve also flown on single-engine piston planes like the Cessna 172 and enjoyed my ride. Anyway, on my few flights on turboprop commercial planes, I noticed that they also have reverse thrust. While I know that for a jet, reverse thrust occurs when the thrust is redirected forward to slow down the plane through doors on the engine cowlings, as is the case with most commercial planes nowadays. But then, how does this happen with turboprops when most of the thrust comes from the props? Do the props change rotational direction?
Turboprop aircraft employ a unique method for reverse thrust, distinct from the traditional thrust reversers found in jet engines. This method, known as the ‘beta range’ or ‘beta mode,’ is a critical component in the operation of turboprops, particularly during landing and ground maneuvers.
Turboprops Do Have Reverse Thrust
The beta range involves adjusting the angle of the propeller blades to change the direction of the exhaust airflow. When a turboprop aircraft is on the ground, the propeller blades are set to a negative angle in the beta range. This adjustment causes the airflow through the propeller disc to be directed partially forward, effectively creating reverse thrust. This mechanism is not only used for slowing down the aircraft during landing but also for maneuvering it on the ground.

The reverse thrust in turboprops is facilitated by a hydro-mechanical system that alters the blade angle of the propeller. By angling the pitch of the propeller, the system can direct thrust forward instead of backward, providing the necessary reverse thrust for various operational needs.
Propeller Blade Dynamics
An interesting aspect of modern propellers is the twist of the blades, where the blade angle is smaller at the tip compared to the root. When reverse thrust is applied, the outer regions of the propeller blades enter a negative angle of attack, producing reverse thrust. However, the root region of the blades does not have a negative angle, ensuring that air is not blown away from the intake in that area. The result is a balanced airflow that allows the compressor to handle the reverse thrust condition efficiently.

It’s important to note that the reverse thrust generated by turboprops is relatively small compared to the forward thrust during flight. Additionally, the speed at which reverse thrust is applied is also lower. Modern compressors in turboprop engines are designed to handle these conditions without difficulty.
To put things into perspective, consider the turboshaft engines used in helicopters during rearward flight. These engines can handle a broader range of speeds in reverse conditions. As an extreme example, Russian aircraft performing tailslides demonstrate that even turbofan engines can cope with reverse airflow, though in a more limited capacity.
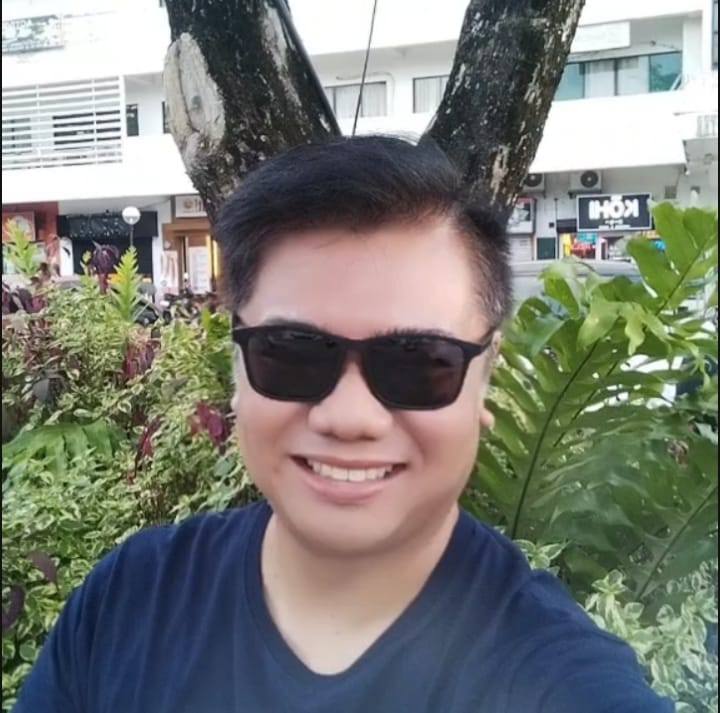
First love never dies. I fell in love with airplanes and aviation when I was a kid. My dream was to become a pilot, but destiny led me to another path: to be an aviation digital media content creator and a small business owner. My passion for aviation inspires me to bring you quality content through my website and social accounts. Aviation is indeed in my blood and blog!