Observing certain large jetliners, such as the Boeing 777 or the classic Boeing 747, from specific vantage points reveals a subtle but deliberate design feature: their wing-mounted engines are not mounted perfectly straight forward. Instead, they exhibit a slight angle, appearing to point marginally towards the aircraft’s main body, the fuselage. This inward angle is neither an accident nor a manufacturing variance; it is a calculated aerodynamic design feature implemented for reasons of efficiency and performance. This intentional angling is technically referred to as “engine toe-in.”
“Engine toe-in” describes the deliberate, minor horizontal angling of jet engines when they are mounted beneath the wings. When one views the aircraft from directly above, the central axis of the engine housing, known as the nacelle, is oriented so that its front intake area points slightly towards the longitudinal centerline of the aircraft’s fuselage. This adjustment is precise, typically involving only a few degrees of angle.
The fundamental engineering purpose behind this toe-in is to optimize the alignment of the engine intakes with the local airflow that the engines actually encounter during flight. This local airflow is distinct from the freestream airflow, which is the undisturbed air far ahead of or away from the aircraft, and it is also generally not parallel to the aircraft’s overall direction of travel. By adjusting the engine’s angle, engineers aim to ensure the intake is facing the oncoming air as squarely as possible at typical cruising conditions.

Examples of this design can be seen in various aircraft models. The Boeing 747, a prominent large commercial jetliner, specifically features a 2-degree toe-in applied to all four of its wing-mounted engines. While a precise numerical value for the Boeing 777’s engine toe-in angle is not consistently published in public technical documents, unlike the widely cited 2-degree angle for the 747, visual evidence and Boeing’s own technical discussions on optimized engine integration confirm its application.
Reason behind the inward engine angle of a Boeing 777
Given the immense size and power of the 777’s engines – some variants are capable of generating over 100,000 pounds of thrust – their precise orientation is critically important. Proper alignment is necessary to effectively manage the complex aerodynamic forces generated and to maximize propulsive efficiency. The very large frontal area characteristic of these modern high-bypass-ratio engines means that even minor misalignments with the actual airflow could result in significant penalties in terms of aerodynamic drag.
The necessity for implementing engine toe-in arises directly from the complex aerodynamic environment an aircraft creates as it traverses through the air. This environment dictates that the airflow encountering an engine mounted under the wing is rarely moving in a direction perfectly parallel to the aircraft’s central axis. Toe-in serves as a corrective measure, specifically designed to counteract the natural tendency of airflow to diverge or flow outwards around the forward and mid-sections of an aircraft’s body, a phenomenon particularly pronounced on aircraft equipped with swept wings.
An aircraft in flight is not merely passing through static or uniformly moving air. Its physical form – including the fuselage, wings, and tail surfaces (empennage) – significantly alters the direction, pressure, and velocity of the air immediately surrounding it. The air that an engine ingests, referred to as the “local airflow,” can be substantially different from the “freestream” air, which represents the undisturbed flow state far ahead of or away from the aircraft.

For optimal engine performance and minimal aerodynamic drag penalties, the engine nacelle must be carefully aligned with this specific local airflow direction, rather than simply with the aircraft’s overall heading or the freestream direction.
Local airflow
As an aircraft moves forward, its nose and the forward section of the fuselage displace the surrounding air. This displacement causes the streamlines of airflow near the fuselage, particularly in the region where the wings attach and extend outwards, to curve outwards, diverging away from the aircraft’s longitudinal axis. If the engines were mounted perfectly parallel to this axis, their intakes would meet this outwardly flowing local air at an angle. This angular impact leads to aerodynamic inefficiencies and an increase in drag.

Toe-in reduces drag
By implementing toe-in, and thereby aligning the engine nacelle more closely with the direction of the local airflow, engineers minimize the angle at which the leading edge of the nacelle meets the oncoming air. This alignment reduces two significant forms of drag: pressure drag and interference drag. Pressure drag results from the difference in pressure distribution around an object not aligned with the flow, while interference drag occurs due to unfavorable aerodynamic interactions between adjacent components, such as the engine nacelle and the wing. If an engine were not toed-in, it would effectively be presenting its intake slightly sideways to the local airflow, generating unnecessary aerodynamic resistance.
Furthermore, maintaining a smooth, uniform flow of air into the engine’s compressor is critical for efficient engine operation. Misalignment of the intake with the local airflow can lead to uneven pressure distribution across the face of the engine fan, which can potentially reduce the amount of thrust the engine produces, increase fuel consumption due to inefficient compression, and in more severe circumstances, contribute to adverse phenomena like compressor stall, which can disrupt engine operation. Toe-in helps ensure that the engine intake captures air with minimal flow distortion.

The combined positive effects of reduced aerodynamic drag on the nacelle and improved efficiency in the engine’s propulsive performance directly result in lower fuel consumption for the aircraft. For commercial airlines, fuel represents a major operational cost component, making even small improvements in fuel efficiency highly desirable and economically impactful. The aerodynamic benefits achieved through engine toe-in are interconnected and compound to enhance overall aircraft performance, with improved fuel efficiency being a primary and crucial outcome.
“Toe-out” on rear-engine aircraft
The engineering principle that engine alignment is determined by the characteristics of the local airflow is powerfully illustrated by contrasting it with the strategy used for rear-mounted engines, which often feature “toe-out.” Aircraft with engines located on the aft fuselage or tail section (examples include the McDonnell Douglas MD-11 or many business jets) often have their engines angled slightly outward, away from the fuselage centerline. This is because the airflow around the tapering rear section of the fuselage tends to be convergent, flowing inward towards the aircraft’s centerline as it passes the tail.
The MD-11’s tail-mounted (Number 2) engine, for instance, is also notably tilted upwards to align with the local airflow characteristics in that specific location and for considerations related to aircraft stability. This contrasting design demonstrates a consistent engineering response: regardless of the mounting location, the engine intake is oriented to face the oncoming local airflow as directly as possible, whether that flow is diverging outwards (requiring toe-in for underwing engines) or converging inwards (requiring toe-out for rear-mounted engines).

The following table summarizes these horizontal alignment strategies based on mounting location:
Engine Mounting Location | Typical Airflow Pattern at Engine | Resulting Horizontal Alignment Strategy | Primary Aerodynamic Reason |
---|---|---|---|
Underwing (e.g., Boeing 777, 747) | Divergent (outboard flow from fuselage & wing sweep) | Toe-In (engines angled inward) | Align intake with local outboard airflow to reduce drag and improve intake efficiency. |
Rear Fuselage/Tail-Mounted (e.g., MD-11, business jets) | Convergent (inward flow around aft body of fuselage) | Toe-Out (engines angled outward) | Align intake with local inward airflow to reduce drag and improve intake efficiency. |
In essence, the seemingly minor inward angle of jet engines on aircraft like the Boeing 777 and 747 is a sophisticated aerodynamic optimization. It is a precise engineering solution to align the engine’s intake with the specific local airflow conditions created by the aircraft’s own movement through the air, leading to reduced drag, improved engine performance, and ultimately, enhanced fuel efficiency – critical factors in modern aviation design.
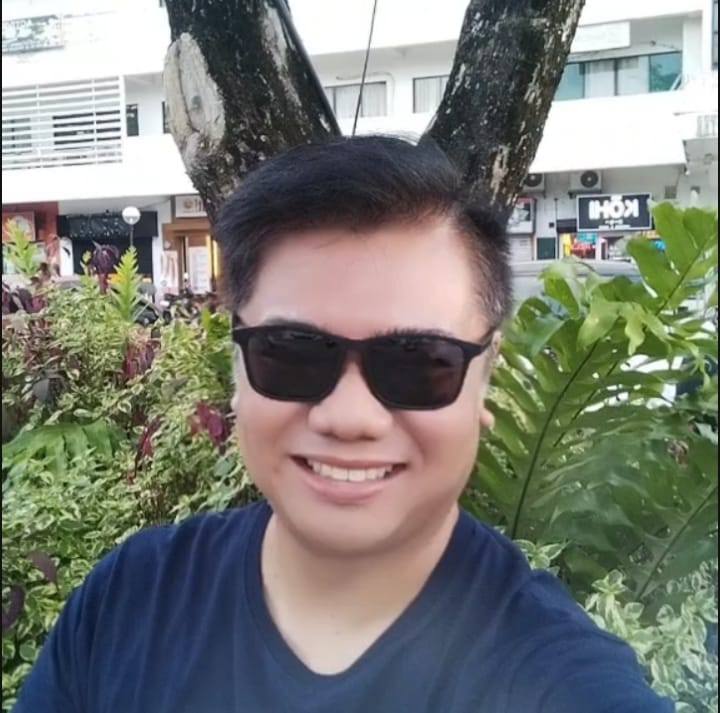
First love never dies. I fell in love with airplanes and aviation when I was a kid. My dream was to become a pilot, but destiny led me to another path: to be an aviation digital media content creator and a small business owner. My passion for aviation inspires me to bring you quality content through my website and social accounts. Aviation is indeed in my blood and blog!